「この工程がボトルネックになっている」といった会話をビジネスシーンで見聞きした経験がある人もいるのではないでしょうか。しかし「ボトルネック」とは何かと質問されると、具体的に回答できない人もいるかと思われます。
そこで本記事では、ビジネスシーンで使用される「ボトルネック」の意味や発生する原因、ボトルネックの発見・改善方法をご紹介します。ボトルネックの意味を知りたい方はもちろん、ボトルネックに悩まされている方にとっても役立つ内容となっていますので、ぜひ最後までお読みください。
なおボトルネック工程の改善には、適材適所の人材配置も重要です。適性のある人を適切な部署やポジションに配置することで、生産性の向上が期待できます。適材適所の人材配置を具体的にどう実現するかは、下記からダウンロードできるお役立ち資料にまとめております。ぜひチェックしてみてください。
【無料ダウンロード】適切な人事異動・配置をするための方法とはそこで本記事では、ビジネスシーンで使用される「ボトルネック」の意味や発生する原因、ボトルネックの発見・改善方法をご紹介します。ボトルネックの意味を知りたい方はもちろん、ボトルネックに悩まされている方にとっても役立つ内容となっていますので、ぜひ最後までお読みください。
なおボトルネック工程の改善には、適材適所の人材配置も重要です。適性のある人を適切な部署やポジションに配置することで、生産性の向上が期待できます。適材適所の人材配置を具体的にどう実現するかは、下記からダウンロードできるお役立ち資料にまとめております。ぜひチェックしてみてください。
▼この記事でわかること
ビジネスにおけるボトルネックとは?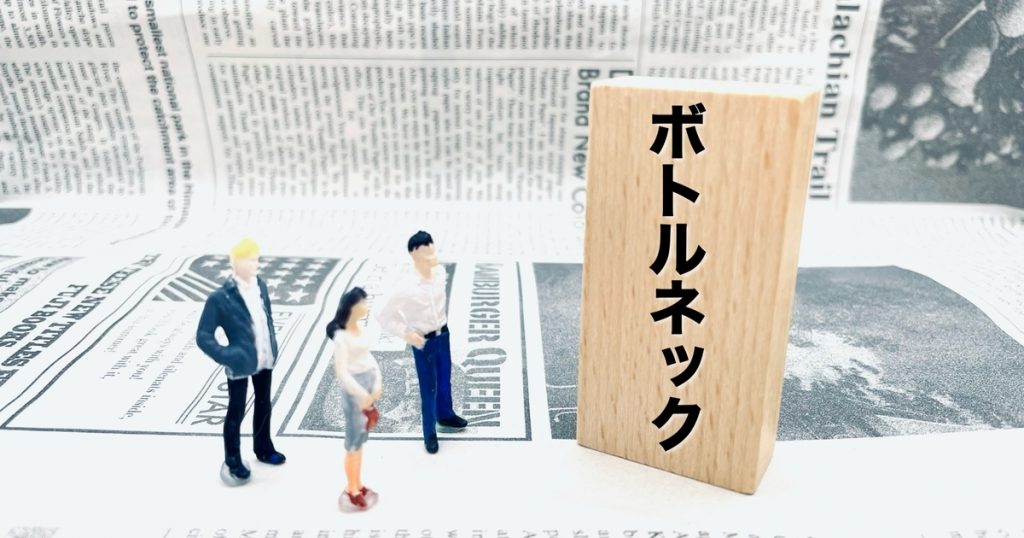
一般的な意味でのボトルネックとは、瓶の首部分のことを指します。胴体部分と比較して首部分は細くなっているのが特徴です。このことからビジネスシーンでは、生産性が低く作業全体の遅延を招いたり、生産性アップを阻害していたりする工程のことを指します。
「人手不足のため他の工程よりも生産性が低い」
「作業が属人化しており、担当者が欠席すると仕事がストップしてしまう」
このような状況を「ボトルネックが発生している」とも表現します。ボトルネックはビジネスにさまざまな悪影響を及ぼすため、早急に発見して改善しましょう。ボトルネックがビジネスに与える悪影響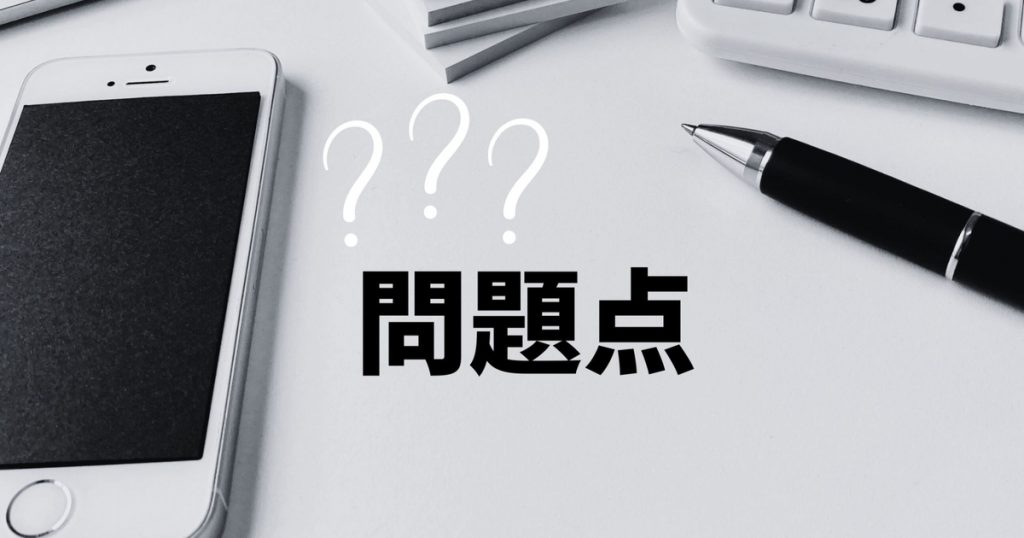
ボトルネックが発生するとビジネスシーンにどのような悪影響を及ぼすのか紹介します。- 生産性が低下する
- 余計なリソースを消費する
- 社内の雰囲気が悪くなる
- 市場での競争力低下につながる
ボトルネックが発生すると、作業全体が遅延してしまい生産性の低下につながります。ボトルネックになっている工程をフォローしようと人員を割くと、無駄なリソースの消費にもつながりかねません。
その結果「あの工程が全体の足を引っ張っている」となってしまい、社内の雰囲気が悪化してしまうこともあるでしょう。その結果、従業員のモチベーションが低下し、さらに生産性が低下する、という悪循環に陥るおそれがあります。
ボトルネックになっている工程を放置しても良いことはありません。可能な限り早急にボトルネックを解消しましょう。ボトルネックが発生する原因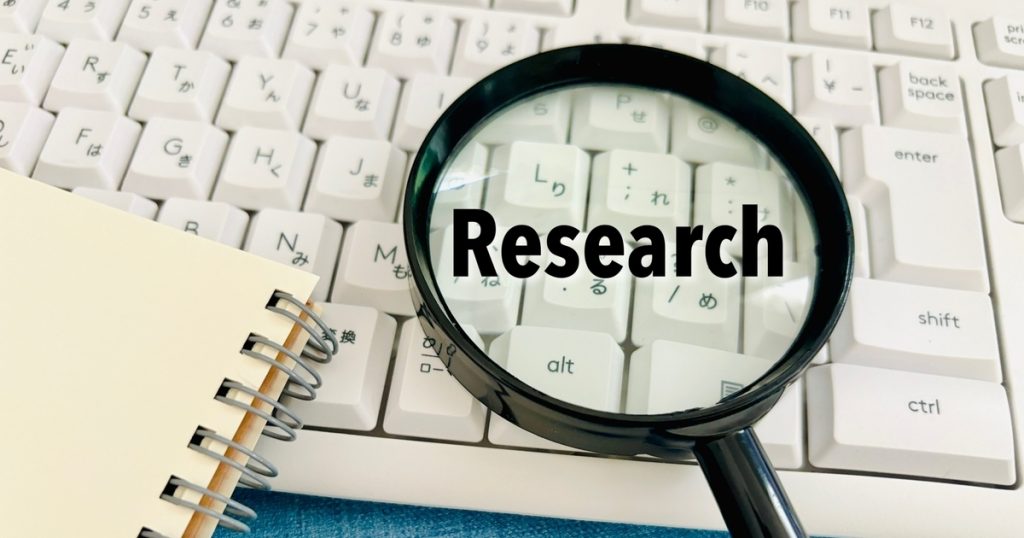
まずはボトルネックが発生する原因についてご紹介します。- 作業フローに無駄がある
- 業務がブラックボックス化している
- 機械化・システム化ができていない
- 十分な人員を確保できていない
- 適材適所の人材配置をできていない
- 適切な仕入れができていない
- 過剰な生産を行っている
どういうことか詳しく解説します。作業フローに無駄がある
作業フローに無駄な工程があるのはボトルネックが発生しやすい状況です。たとえばデジタル化を行わずに手作業で仕事を行っていたり、必ずしも生産に必要でない無駄な作業を行っていたりすることが挙げられます。
「うちは昔からこのやり方で仕事をしてきたから」
「とにかく目の前の仕事だけをこなせ」
このような考え方を持っていてはボトルネックを解消しにくいでしょう。こだわるべき重要なポイントは残しつつ、作業に無駄はないか・より良い方法はないか、継続的な見直しを行うことが大切です。業務がブラックボックス化している
「あの人がいないと作業できない」
「仕事の進め方が個人任せになっている」
このように、どのような仕事を行っているのか外部から客観的に分からない、いわゆる業務のブラックボックス化も問題です。
業務のブラックボックス化していると、作業のクオリティが担当者の能力に依存したり担当者が欠席したりすることで生産性が大きく下がりかねません。その結果、ボトルネックが発生してしまい会社全体の生産性が大きく下がります。機械化・システム化ができていない
紙やハンコといったアナログ業務も、作業のボトルネックになっている可能性があります。
たとえば日報や報告書を電子化すれば、情報を効率的に共有したり保管する際の手間がかかりにくくなったりします。ハンコも使わないか代わりに電子印を利用するなど対応すれば、業務の生産性が上がるでしょう。
ただし作業内容によってはアナログ作業の方が向いている場合もあります。たとえば工場で作業を行っており手が汚れた状態で、パソコンやタブレットを快適に操作するのは難しいでしょう。無理に電子化してしまうとすぐに機械が壊れたり、うまく利用できずに効率が悪くなったりと、かえってコストがかかってしまいます。十分な人員を確保できていない
スタッフを十分に確保できず生産能力面でのボトルネックが発生する場合もあります。世間では「人手不足」といったテーマのニュースを多く見聞きするようになりました。実際にデータでも、人手不足であることがうかがえます。
下図は厚生労働省が公開している資料を引用したものです。人手不足に関連した倒産は増加傾向にあり、特に2023年は「人件費高騰による倒産」が大幅増となりました。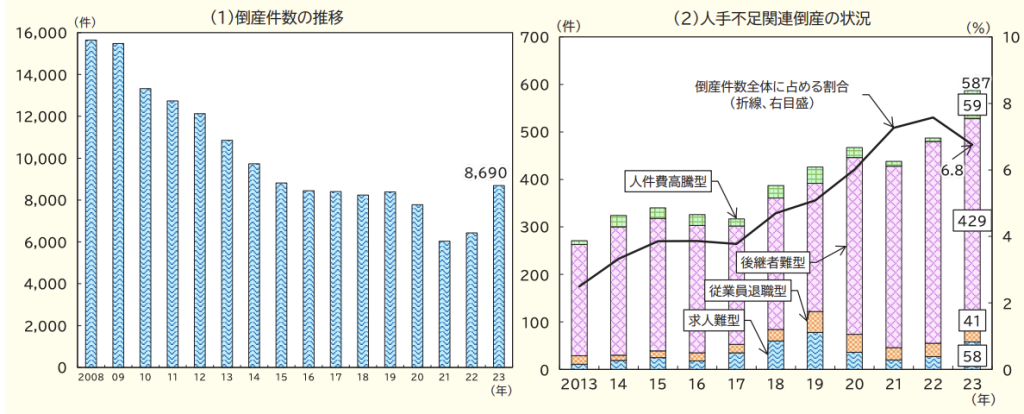
人件費の高騰はもちろんのこと、少子化による働き手の構造的な不足も要因として挙げられます。このような理由からスタッフを十分に採用できず、ボトルネックを解消できないパターンもあります。適材適所の人材配置をできていない
従業員の適性を活かせる部署に配属できておらず、能力を十分発揮できずにボトルネックが発生している場合もあります。
人には向き不向きがあります。たとえば現場で手を動かして働くのが好きな人もいれば、リーダーシップを発揮してチームを引っ張ったり仕組みを構築したりするのが好きな人もいるでしょう。
当たり前のことと思われるかもしれませんが、個人の適性を考慮した人材配置を実現できている企業は、多くはありません。なぜなら従業員の適性を一人ひとり見極めるのは手間と時間がかかるうえに、精度が良いのかどうか分かりにくいからです。
そこで人材アセスメントツール「ミイダス」では、適材適所の人材配置を実現するためのノウハウをまとめたお役立ち資料をご用意しました。下記から誰でも無料でダウンロードできるので、ぜひチェックしてください。
【無料ダウンロード】適切な人事異動・配置をするための方法とは適切な仕入れができていない
在庫を抱えすぎたり仕入れが少なすぎたりするのも、ボトルネックが発生する要因です。
たとえば在庫を抱えすぎてしまうと保管するスペースを圧迫してしまい、作業場まで在庫が溢れてしまうおそれがあります。そうなると在庫が作業の邪魔になり、生産性が落ちてしまいかねません。
また仕入れが少なすぎると生産そのものを続行しにくくなり、こちらもボトルネックの発生につながります。ボトルネックを発生させないためにも適切な量の仕入れを行うことが大切です。過剰な生産を行っている
需要を超えた過剰な生産を行ってしまうのもボトルネックが発生する要因です。
たとえば出荷する以上に製品を作りすぎてしまうと、在庫を保管するスペースを圧迫してしまいます。すると仕入れと同様、作業スペースが圧迫されてしまい生産性が低下するおそれがあります。需要を予測して適切な量の生産を行うことが重要です。ボトルネック工程の見つけ方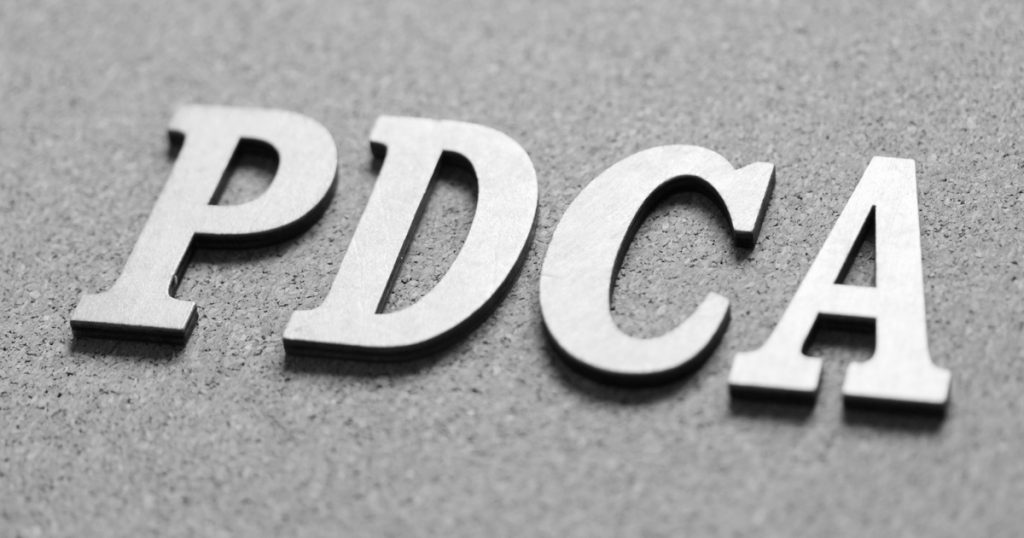
ボトルネック工程を発見する主な方法をご紹介します。- 業務フローを可視化する
- データを分析して問題箇所を特定する
- 実際に現場を確認して問題箇所を特定する
それぞれ詳しく解説します。業務フローを可視化する
業務の流れの可視化は下記のようなメリットがあり、ボトルネックを解消できる可能性があります。- 工程ごとの関係性を可視化でき、無駄な工程を発見しやすい
- どの工程がどこに影響をするか視覚的に把握しやすくなり、工程の効率化を行いやすい
- 自分の担当工程がどのような影響を及ぼすのか把握しやすくなり、部署間の連携を強化しやすい
業務フローの可視化は、問題となっている工程の発見や効率化を行ううえで役立ちます。まずは作業の全体像を把握するためにも、業務フローを書き出してみましょう。紙やホワイトボードに書き出したり、タブレットのような手書き対応のデバイスにまとめたりするのがおすすめです。データを分析して問題箇所を特定する
数字を根拠に問題箇所を発見するのも、ボトルネックを見つけるうえで役立ちます。
たとえば組立工程で、1時間当たり100個の製品ができると仮定しましょう。このとき製品の部品を製造する工程で、1時間あたり30個しか生産できていないとわかりました。すると、部品の製造工程がボトルネックになっていると特定できます。実際に現場を確認して問題箇所を特定する
現場に足を運んで問題はないか確認するのも、ボトルネックを特定するうえで有用です。
データ上は問題なくても、実際に製造現場を見てみると暇そうな従業員がいたり使われていない設備を発見できたりします。TOC理論を活用したボトルネック工程の改善方法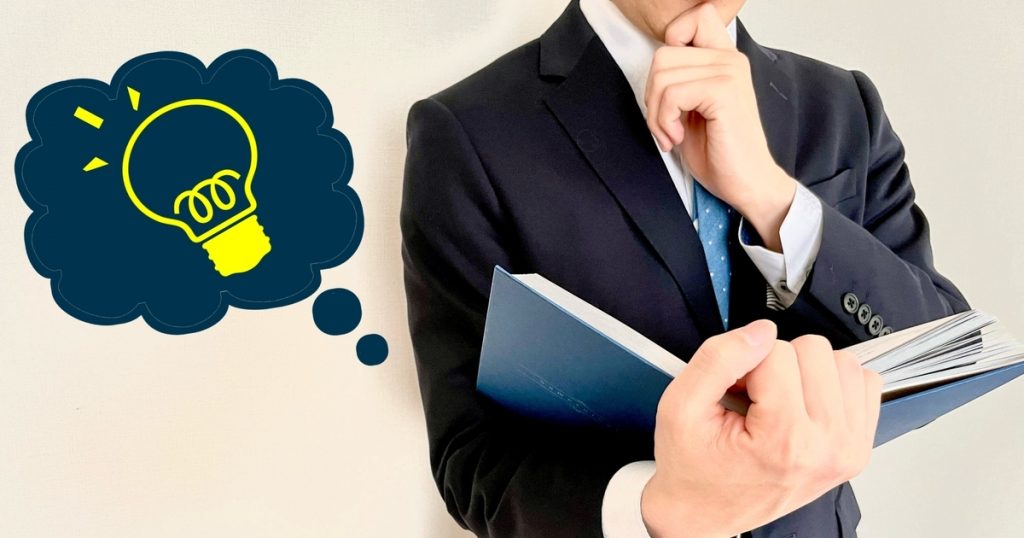
ボトルネックを改善する方法として有名なものに「TOC理論(制約理論)」というものがあります。TOC理論は「業務フローの制約条件(≒ボトルネック)を解消して全体最適化を実現できる」ことを示している考え方です。
TOC理論では下記の流れで改善を行うことで、ボトルネックを解消できると提唱しています。1. ボトルネックとなっている工程を特定する
2. ボトルネック工程のパフォーマンスを向上させる
3. 他工程をボトルネック工程に合わせる
4. ボトルネック工程をてこ入れする
5. 新たなボトルネック工程を発見・改善する具体的にどのようなことを行うのか解説します。ボトルネックとなっている工程を特定する
まずはボトルネックとなっている工程を特定します。
上述したようにデータを確認したり実際に現場を確認したりして、問題のある工程を発見しましょう。ボトルネック工程のパフォーマンスを向上させる
ボトルネック工程を発見したら、既存の設備・人員のままパフォーマンスを向上させるための方法を考えます。- 待ち時間が発生している人はいないか
- 動いていない設備、待ち時間が発生している設備はないか
- 無駄な作業が発生していないか
上記の観点から、既存の設備・人員のままボトルネックを解消できないか検討しましょう。データをもとに仮説を立てたり、実際に現場へ足を運んだりすることで、パフォーマンス向上のきっかけを掴める可能性があります。他工程をボトルネック工程に合わせる
ボトルネックを現状対応できる範囲で改善できたら、次は他の工程をボトルネック工程に合わせます。たとえば現状の生産量は下記のとおりだと仮定しましょう。- 部品生産:15個/時間
- 製品組立:30個/時間
- 検品:50個/時間
このとき、ボトルネックとなっている部品生産の「15個/時間」まで、部品組立と検品の生産性を合わせます。これによって生まれた余剰能力を、ボトルネック工程の解消に活用します。ボトルネック工程をてこ入れする
余った余剰能力を活用して、ボトルネック工程にテコ入れを行います。
具体的にはボトルネック工程の従業員を増員したり、古い設備やシステムを更新したりします。これによって生産性が向上し、ボトルネックの解消が期待できるでしょう。新たなボトルネック工程を発見・改善する
ボトルネック工程を解消できたら、次は新たなボトルネック工程を発見して改善できないか検討してみましょう。たとえば下記の場合は「部品組立」が新たなボトルネック工程といえます。- 部品生産:60個/時間
- 製品組立:30個/時間
- 検品:50個/時間
ボトルネック工程を発見したら再び「既存設備・人員のままパフォーマンスを向上させる」「他工程をボトルネック工程に合わせる」「てこ入れを行う」といった方法で改善を進めていきます。
これを繰り返すことで全体の生産能力が底上げされるはずです。ボトルネック工程をてこ入れ・改善する方法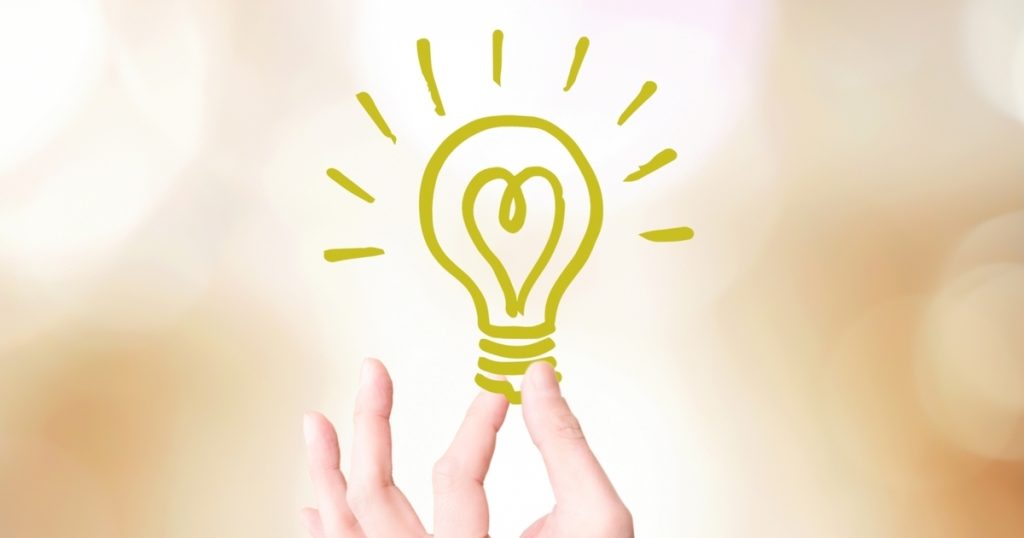
ここからはボトルネック工程をどのようにテコ入れして改善するのか、具体的な方法をご紹介します。- 適材適所の人材配置を行い一人ひとりのパフォーマンスを引き出す
- 新しい機械やシステムを導入して業務を効率化する
- より効率的な作業手順がないか検討して改善を試みる
- 人材を育成して一人あたりの生産性を高める
それぞれ詳しく解説します。適材適所の人材配置を行い一人ひとりのパフォーマンスを引き出す
ボトルネックを解消する方法の一つに、従業員のパフォーマンスを引き出すことが挙げられます。特に従業員一人ひとりの適性に合った人材配置を行っていれば、仕事へのモチベーションが向上したり成長速度が早まったりするはずです。
とはいえ一人ひとりの適性を見極めて人材配置を行うのは難しいかもしれません。担当した人事の能力によっても、成果が大きく左右されるでしょう。そこで人材アセスメントツール「ミイダス」では、適材適所の人材配置を実現するための具体的な方法についてまとめたお役立ち資料をご用意しております。
人事個人のスキルに依存しない、客観的に従業員の適性を見極める方法も紹介しています。適材適所の人材配置を実現するうえで役に立つ内容となっておりますので、ぜひチェックしてください。
【無料ダウンロード】適切な人事異動・配置をするための方法とは新しい機械やシステムを導入して業務を効率化する
新しいシステムや機械設備を導入するのも、ボトルネックを解消するうえで重要です。
何十年も使ってきた設備は、最新の設備と比較して生産性が低かったりトラブルが発生しやすかったりするものです。またパソコンをはじめとしたさまざまなデバイスのシステムを更新することでも、生産性の向上が期待できるでしょう。
工程を機械化すれば大量生産しやすくなるうえ、システム化・デジタル化を行えば情報共有の効率化や事務作業の生産性向上も期待できます。より効率的な作業手順がないか検討して改善を試みる
システム化や機械化に頼らず、より効率的な手順がないか検討してみることも大切です。
たとえば決裁フローが「部下→課長→部長」となっている場合、「部下→課長」または「部下→部長」に変更すれば、意思決定のスピードが向上するはずです。また「製造→検査→組立→検査→出荷」という作業フローの場合、「製造→組立→検査→出荷」という流れに変更するのも、効率化に役立ちます。
ただし必要な工程まで省略してしまうと、消費者からのクレームや商品の自主回収といったトラブルに発展してしまいかねません。省略できる工程かどうか見極めることも大切です。
無駄な作業を省いたり工夫次第ですぐに生産性が上がったりする方法がないか、検討してみましょう。人材を育成して一人あたりの生産性を高める
従業員を育成して生産性を向上させることも重要です。
たとえば工場作業の場合、OJTに加えて動画研修を実施したり、手順をマニュアル化して読ませたりする、といった方法で人材育成の質と量を向上できるでしょう。従業員が担当している仕事について理解を深めれば、生産性も向上するはずです。
従業員の教育をより効率的に・効果的に行う方法がないか検討してみましょう。ボトルネック工程を改善してビジネスを成長させよう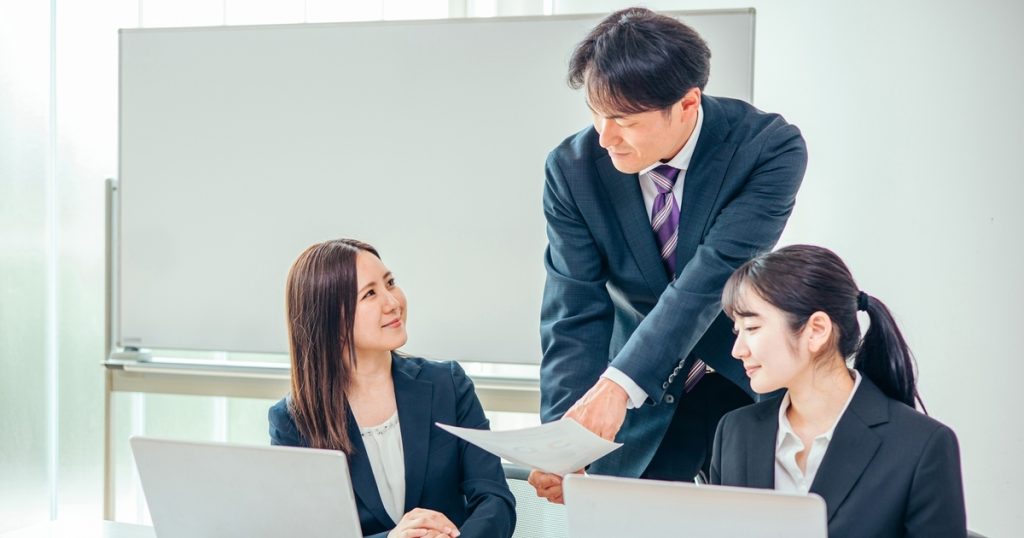
本記事ではビジネスにおけるボトルネックの意味や発生する原因、改善方法などをご紹介しました。
ボトルネックを解消できないと生産性が向上しにくく、企業の成長が鈍化してしまいかねません。ビジネスチャンスを逃さないためにも、ボトルネックの発見〜改善活動は継続的に行いましょう。
ボトルネックを解消するにはさまざまな方法がありますが、特に「適材適所の人材配置を実現する」ことをおすすめします。ボトルネックとなっている工程に適性のある人材を配置することで、作業効率が上がりボトルネックが解消する可能性があるためです。
とはいえ従業員の適性を一人ひとり見極めるのは手間がかかりますし、何より具体的にどうすれば良いのかお悩みかもしれません。そこでミイダスでは、適材適所の人材配置を実現するためのノウハウをまとめたお役立ち資料をご用意しました。下記からどなたでも無料でダウンロードできますので、ぜひチェックしてください。
【無料ダウンロード】適切な人事異動・配置をするための方法とは
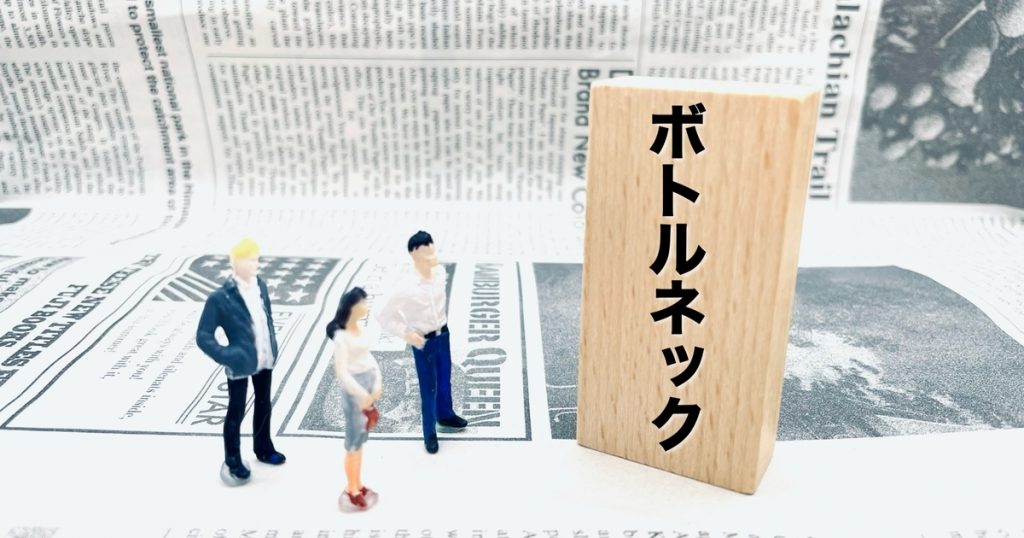
「人手不足のため他の工程よりも生産性が低い」
「作業が属人化しており、担当者が欠席すると仕事がストップしてしまう」
このような状況を「ボトルネックが発生している」とも表現します。ボトルネックはビジネスにさまざまな悪影響を及ぼすため、早急に発見して改善しましょう。
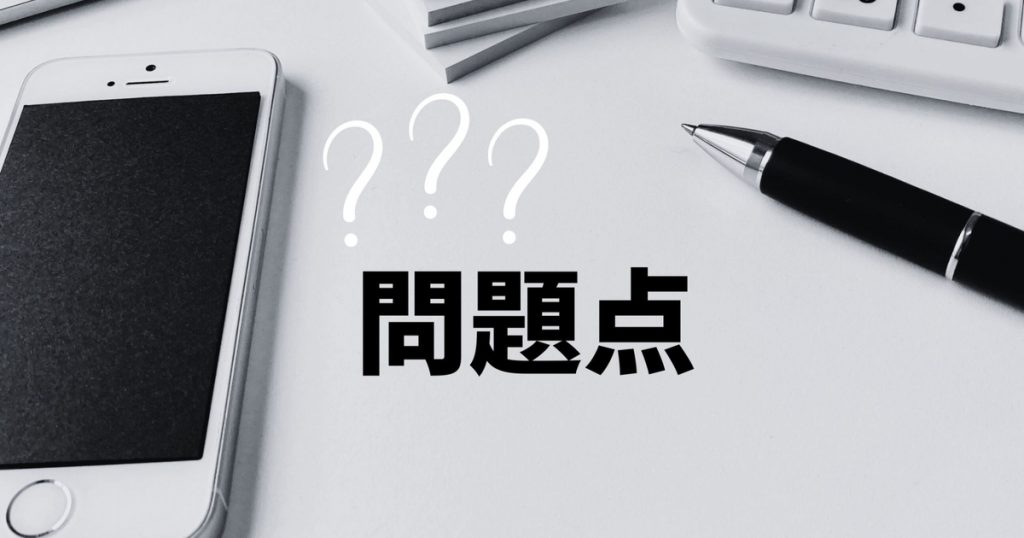
ボトルネックが発生するとビジネスシーンにどのような悪影響を及ぼすのか紹介します。
- 生産性が低下する
- 余計なリソースを消費する
- 社内の雰囲気が悪くなる
- 市場での競争力低下につながる
ボトルネックが発生すると、作業全体が遅延してしまい生産性の低下につながります。ボトルネックになっている工程をフォローしようと人員を割くと、無駄なリソースの消費にもつながりかねません。
その結果「あの工程が全体の足を引っ張っている」となってしまい、社内の雰囲気が悪化してしまうこともあるでしょう。その結果、従業員のモチベーションが低下し、さらに生産性が低下する、という悪循環に陥るおそれがあります。
ボトルネックになっている工程を放置しても良いことはありません。可能な限り早急にボトルネックを解消しましょう。
その結果「あの工程が全体の足を引っ張っている」となってしまい、社内の雰囲気が悪化してしまうこともあるでしょう。その結果、従業員のモチベーションが低下し、さらに生産性が低下する、という悪循環に陥るおそれがあります。
ボトルネックになっている工程を放置しても良いことはありません。可能な限り早急にボトルネックを解消しましょう。
ボトルネックが発生する原因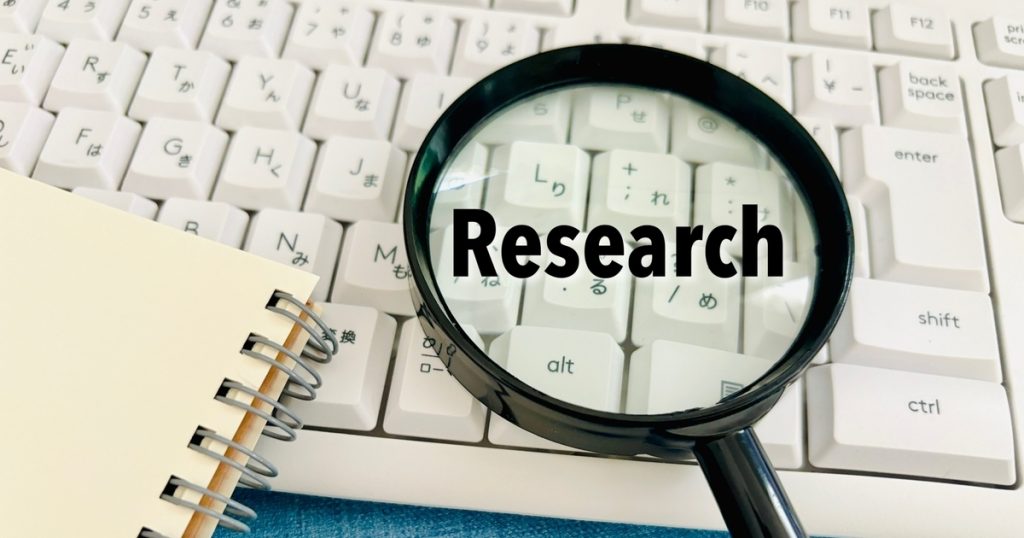
まずはボトルネックが発生する原因についてご紹介します。- 作業フローに無駄がある
- 業務がブラックボックス化している
- 機械化・システム化ができていない
- 十分な人員を確保できていない
- 適材適所の人材配置をできていない
- 適切な仕入れができていない
- 過剰な生産を行っている
どういうことか詳しく解説します。作業フローに無駄がある
作業フローに無駄な工程があるのはボトルネックが発生しやすい状況です。たとえばデジタル化を行わずに手作業で仕事を行っていたり、必ずしも生産に必要でない無駄な作業を行っていたりすることが挙げられます。
「うちは昔からこのやり方で仕事をしてきたから」
「とにかく目の前の仕事だけをこなせ」
このような考え方を持っていてはボトルネックを解消しにくいでしょう。こだわるべき重要なポイントは残しつつ、作業に無駄はないか・より良い方法はないか、継続的な見直しを行うことが大切です。業務がブラックボックス化している
「あの人がいないと作業できない」
「仕事の進め方が個人任せになっている」
このように、どのような仕事を行っているのか外部から客観的に分からない、いわゆる業務のブラックボックス化も問題です。
業務のブラックボックス化していると、作業のクオリティが担当者の能力に依存したり担当者が欠席したりすることで生産性が大きく下がりかねません。その結果、ボトルネックが発生してしまい会社全体の生産性が大きく下がります。機械化・システム化ができていない
紙やハンコといったアナログ業務も、作業のボトルネックになっている可能性があります。
たとえば日報や報告書を電子化すれば、情報を効率的に共有したり保管する際の手間がかかりにくくなったりします。ハンコも使わないか代わりに電子印を利用するなど対応すれば、業務の生産性が上がるでしょう。
ただし作業内容によってはアナログ作業の方が向いている場合もあります。たとえば工場で作業を行っており手が汚れた状態で、パソコンやタブレットを快適に操作するのは難しいでしょう。無理に電子化してしまうとすぐに機械が壊れたり、うまく利用できずに効率が悪くなったりと、かえってコストがかかってしまいます。十分な人員を確保できていない
スタッフを十分に確保できず生産能力面でのボトルネックが発生する場合もあります。世間では「人手不足」といったテーマのニュースを多く見聞きするようになりました。実際にデータでも、人手不足であることがうかがえます。
下図は厚生労働省が公開している資料を引用したものです。人手不足に関連した倒産は増加傾向にあり、特に2023年は「人件費高騰による倒産」が大幅増となりました。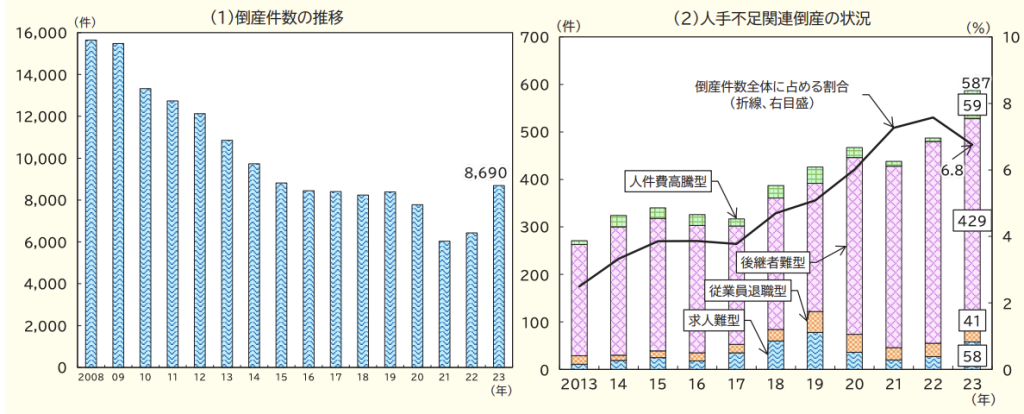
人件費の高騰はもちろんのこと、少子化による働き手の構造的な不足も要因として挙げられます。このような理由からスタッフを十分に採用できず、ボトルネックを解消できないパターンもあります。適材適所の人材配置をできていない
従業員の適性を活かせる部署に配属できておらず、能力を十分発揮できずにボトルネックが発生している場合もあります。
人には向き不向きがあります。たとえば現場で手を動かして働くのが好きな人もいれば、リーダーシップを発揮してチームを引っ張ったり仕組みを構築したりするのが好きな人もいるでしょう。
当たり前のことと思われるかもしれませんが、個人の適性を考慮した人材配置を実現できている企業は、多くはありません。なぜなら従業員の適性を一人ひとり見極めるのは手間と時間がかかるうえに、精度が良いのかどうか分かりにくいからです。
そこで人材アセスメントツール「ミイダス」では、適材適所の人材配置を実現するためのノウハウをまとめたお役立ち資料をご用意しました。下記から誰でも無料でダウンロードできるので、ぜひチェックしてください。
【無料ダウンロード】適切な人事異動・配置をするための方法とは適切な仕入れができていない
在庫を抱えすぎたり仕入れが少なすぎたりするのも、ボトルネックが発生する要因です。
たとえば在庫を抱えすぎてしまうと保管するスペースを圧迫してしまい、作業場まで在庫が溢れてしまうおそれがあります。そうなると在庫が作業の邪魔になり、生産性が落ちてしまいかねません。
また仕入れが少なすぎると生産そのものを続行しにくくなり、こちらもボトルネックの発生につながります。ボトルネックを発生させないためにも適切な量の仕入れを行うことが大切です。過剰な生産を行っている
需要を超えた過剰な生産を行ってしまうのもボトルネックが発生する要因です。
たとえば出荷する以上に製品を作りすぎてしまうと、在庫を保管するスペースを圧迫してしまいます。すると仕入れと同様、作業スペースが圧迫されてしまい生産性が低下するおそれがあります。需要を予測して適切な量の生産を行うことが重要です。ボトルネック工程の見つけ方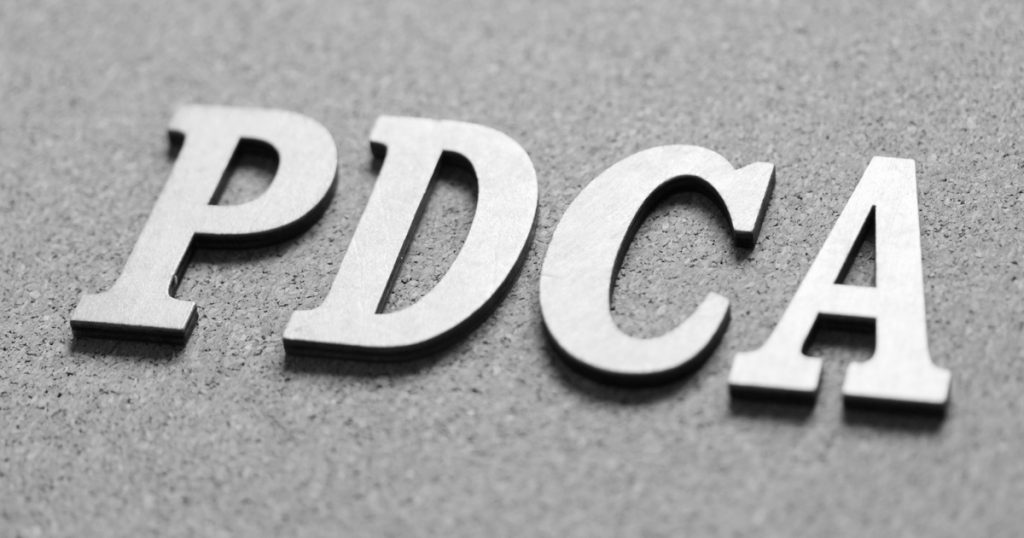
ボトルネック工程を発見する主な方法をご紹介します。- 業務フローを可視化する
- データを分析して問題箇所を特定する
- 実際に現場を確認して問題箇所を特定する
それぞれ詳しく解説します。業務フローを可視化する
業務の流れの可視化は下記のようなメリットがあり、ボトルネックを解消できる可能性があります。- 工程ごとの関係性を可視化でき、無駄な工程を発見しやすい
- どの工程がどこに影響をするか視覚的に把握しやすくなり、工程の効率化を行いやすい
- 自分の担当工程がどのような影響を及ぼすのか把握しやすくなり、部署間の連携を強化しやすい
業務フローの可視化は、問題となっている工程の発見や効率化を行ううえで役立ちます。まずは作業の全体像を把握するためにも、業務フローを書き出してみましょう。紙やホワイトボードに書き出したり、タブレットのような手書き対応のデバイスにまとめたりするのがおすすめです。データを分析して問題箇所を特定する
数字を根拠に問題箇所を発見するのも、ボトルネックを見つけるうえで役立ちます。
たとえば組立工程で、1時間当たり100個の製品ができると仮定しましょう。このとき製品の部品を製造する工程で、1時間あたり30個しか生産できていないとわかりました。すると、部品の製造工程がボトルネックになっていると特定できます。実際に現場を確認して問題箇所を特定する
現場に足を運んで問題はないか確認するのも、ボトルネックを特定するうえで有用です。
データ上は問題なくても、実際に製造現場を見てみると暇そうな従業員がいたり使われていない設備を発見できたりします。TOC理論を活用したボトルネック工程の改善方法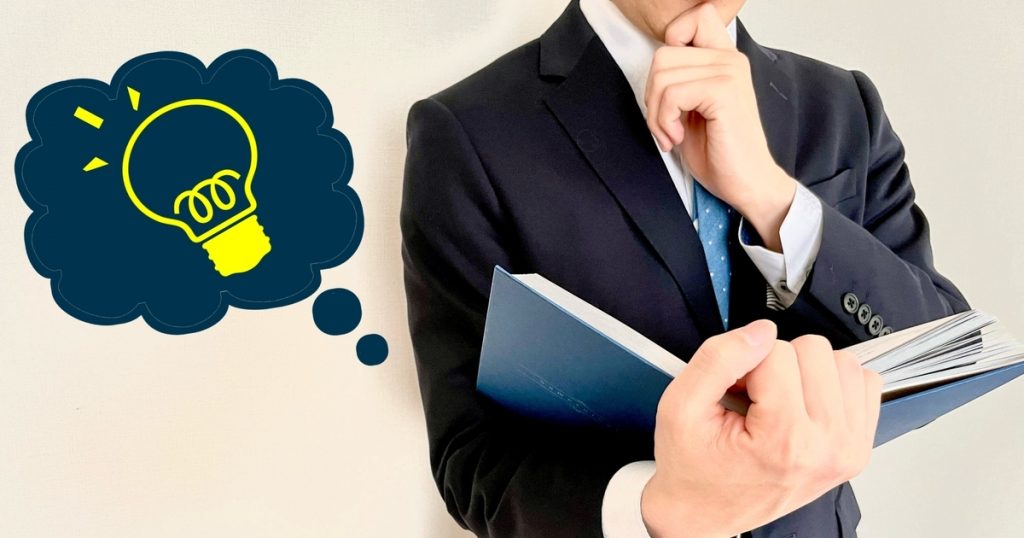
ボトルネックを改善する方法として有名なものに「TOC理論(制約理論)」というものがあります。TOC理論は「業務フローの制約条件(≒ボトルネック)を解消して全体最適化を実現できる」ことを示している考え方です。
TOC理論では下記の流れで改善を行うことで、ボトルネックを解消できると提唱しています。1. ボトルネックとなっている工程を特定する
2. ボトルネック工程のパフォーマンスを向上させる
3. 他工程をボトルネック工程に合わせる
4. ボトルネック工程をてこ入れする
5. 新たなボトルネック工程を発見・改善する具体的にどのようなことを行うのか解説します。ボトルネックとなっている工程を特定する
まずはボトルネックとなっている工程を特定します。
上述したようにデータを確認したり実際に現場を確認したりして、問題のある工程を発見しましょう。ボトルネック工程のパフォーマンスを向上させる
ボトルネック工程を発見したら、既存の設備・人員のままパフォーマンスを向上させるための方法を考えます。- 待ち時間が発生している人はいないか
- 動いていない設備、待ち時間が発生している設備はないか
- 無駄な作業が発生していないか
上記の観点から、既存の設備・人員のままボトルネックを解消できないか検討しましょう。データをもとに仮説を立てたり、実際に現場へ足を運んだりすることで、パフォーマンス向上のきっかけを掴める可能性があります。他工程をボトルネック工程に合わせる
ボトルネックを現状対応できる範囲で改善できたら、次は他の工程をボトルネック工程に合わせます。たとえば現状の生産量は下記のとおりだと仮定しましょう。- 部品生産:15個/時間
- 製品組立:30個/時間
- 検品:50個/時間
このとき、ボトルネックとなっている部品生産の「15個/時間」まで、部品組立と検品の生産性を合わせます。これによって生まれた余剰能力を、ボトルネック工程の解消に活用します。ボトルネック工程をてこ入れする
余った余剰能力を活用して、ボトルネック工程にテコ入れを行います。
具体的にはボトルネック工程の従業員を増員したり、古い設備やシステムを更新したりします。これによって生産性が向上し、ボトルネックの解消が期待できるでしょう。新たなボトルネック工程を発見・改善する
ボトルネック工程を解消できたら、次は新たなボトルネック工程を発見して改善できないか検討してみましょう。たとえば下記の場合は「部品組立」が新たなボトルネック工程といえます。- 部品生産:60個/時間
- 製品組立:30個/時間
- 検品:50個/時間
ボトルネック工程を発見したら再び「既存設備・人員のままパフォーマンスを向上させる」「他工程をボトルネック工程に合わせる」「てこ入れを行う」といった方法で改善を進めていきます。
これを繰り返すことで全体の生産能力が底上げされるはずです。ボトルネック工程をてこ入れ・改善する方法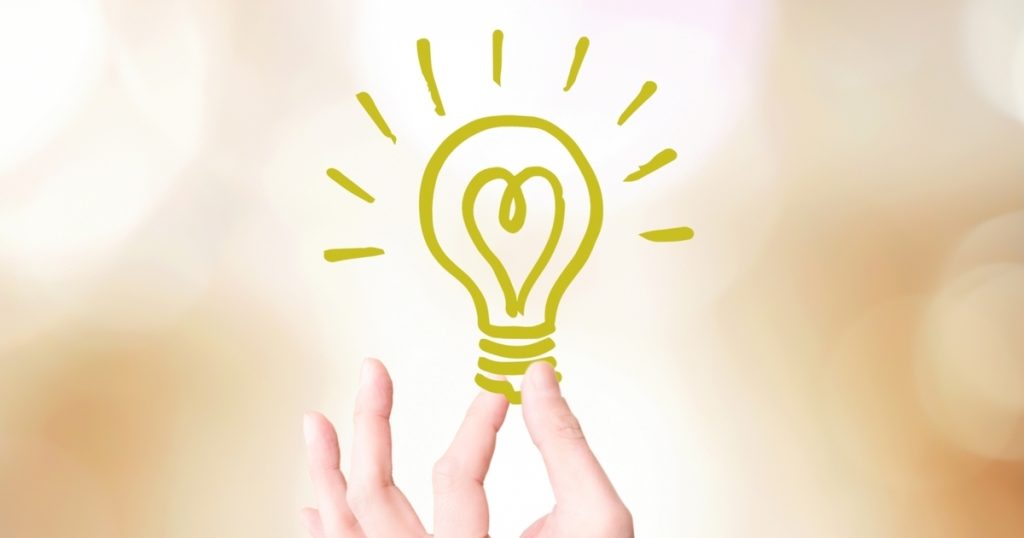
ここからはボトルネック工程をどのようにテコ入れして改善するのか、具体的な方法をご紹介します。- 適材適所の人材配置を行い一人ひとりのパフォーマンスを引き出す
- 新しい機械やシステムを導入して業務を効率化する
- より効率的な作業手順がないか検討して改善を試みる
- 人材を育成して一人あたりの生産性を高める
それぞれ詳しく解説します。適材適所の人材配置を行い一人ひとりのパフォーマンスを引き出す
ボトルネックを解消する方法の一つに、従業員のパフォーマンスを引き出すことが挙げられます。特に従業員一人ひとりの適性に合った人材配置を行っていれば、仕事へのモチベーションが向上したり成長速度が早まったりするはずです。
とはいえ一人ひとりの適性を見極めて人材配置を行うのは難しいかもしれません。担当した人事の能力によっても、成果が大きく左右されるでしょう。そこで人材アセスメントツール「ミイダス」では、適材適所の人材配置を実現するための具体的な方法についてまとめたお役立ち資料をご用意しております。
人事個人のスキルに依存しない、客観的に従業員の適性を見極める方法も紹介しています。適材適所の人材配置を実現するうえで役に立つ内容となっておりますので、ぜひチェックしてください。
【無料ダウンロード】適切な人事異動・配置をするための方法とは新しい機械やシステムを導入して業務を効率化する
新しいシステムや機械設備を導入するのも、ボトルネックを解消するうえで重要です。
何十年も使ってきた設備は、最新の設備と比較して生産性が低かったりトラブルが発生しやすかったりするものです。またパソコンをはじめとしたさまざまなデバイスのシステムを更新することでも、生産性の向上が期待できるでしょう。
工程を機械化すれば大量生産しやすくなるうえ、システム化・デジタル化を行えば情報共有の効率化や事務作業の生産性向上も期待できます。より効率的な作業手順がないか検討して改善を試みる
システム化や機械化に頼らず、より効率的な手順がないか検討してみることも大切です。
たとえば決裁フローが「部下→課長→部長」となっている場合、「部下→課長」または「部下→部長」に変更すれば、意思決定のスピードが向上するはずです。また「製造→検査→組立→検査→出荷」という作業フローの場合、「製造→組立→検査→出荷」という流れに変更するのも、効率化に役立ちます。
ただし必要な工程まで省略してしまうと、消費者からのクレームや商品の自主回収といったトラブルに発展してしまいかねません。省略できる工程かどうか見極めることも大切です。
無駄な作業を省いたり工夫次第ですぐに生産性が上がったりする方法がないか、検討してみましょう。人材を育成して一人あたりの生産性を高める
従業員を育成して生産性を向上させることも重要です。
たとえば工場作業の場合、OJTに加えて動画研修を実施したり、手順をマニュアル化して読ませたりする、といった方法で人材育成の質と量を向上できるでしょう。従業員が担当している仕事について理解を深めれば、生産性も向上するはずです。
従業員の教育をより効率的に・効果的に行う方法がないか検討してみましょう。ボトルネック工程を改善してビジネスを成長させよう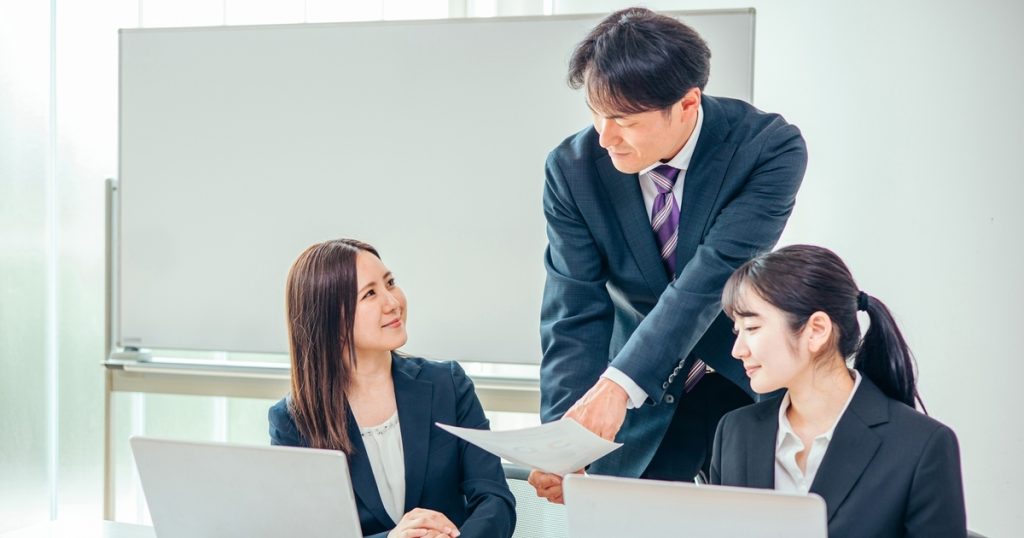
本記事ではビジネスにおけるボトルネックの意味や発生する原因、改善方法などをご紹介しました。
ボトルネックを解消できないと生産性が向上しにくく、企業の成長が鈍化してしまいかねません。ビジネスチャンスを逃さないためにも、ボトルネックの発見〜改善活動は継続的に行いましょう。
ボトルネックを解消するにはさまざまな方法がありますが、特に「適材適所の人材配置を実現する」ことをおすすめします。ボトルネックとなっている工程に適性のある人材を配置することで、作業効率が上がりボトルネックが解消する可能性があるためです。
とはいえ従業員の適性を一人ひとり見極めるのは手間がかかりますし、何より具体的にどうすれば良いのかお悩みかもしれません。そこでミイダスでは、適材適所の人材配置を実現するためのノウハウをまとめたお役立ち資料をご用意しました。下記からどなたでも無料でダウンロードできますので、ぜひチェックしてください。
【無料ダウンロード】適切な人事異動・配置をするための方法とは
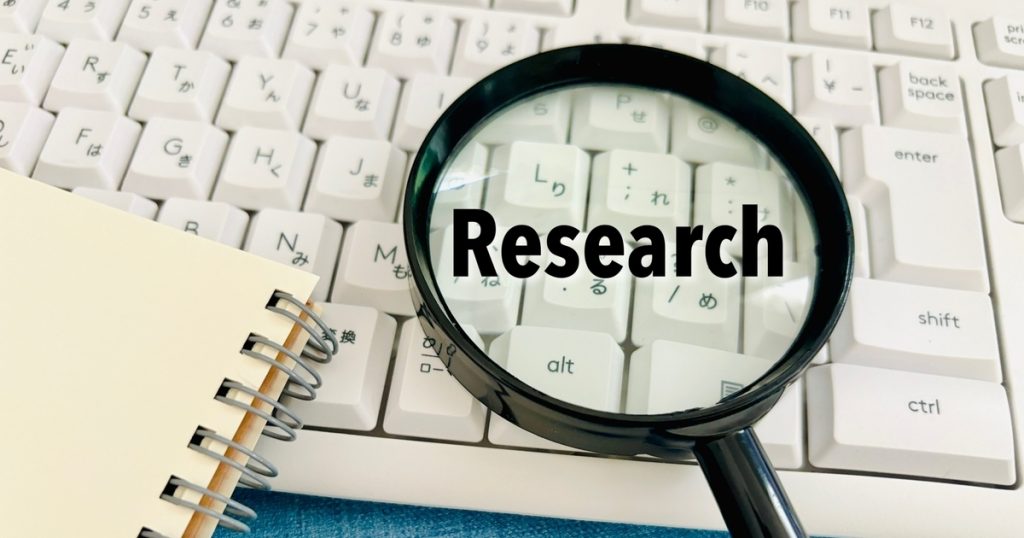
「うちは昔からこのやり方で仕事をしてきたから」
「とにかく目の前の仕事だけをこなせ」
このような考え方を持っていてはボトルネックを解消しにくいでしょう。こだわるべき重要なポイントは残しつつ、作業に無駄はないか・より良い方法はないか、継続的な見直しを行うことが大切です。
「仕事の進め方が個人任せになっている」
このように、どのような仕事を行っているのか外部から客観的に分からない、いわゆる業務のブラックボックス化も問題です。
業務のブラックボックス化していると、作業のクオリティが担当者の能力に依存したり担当者が欠席したりすることで生産性が大きく下がりかねません。その結果、ボトルネックが発生してしまい会社全体の生産性が大きく下がります。
たとえば日報や報告書を電子化すれば、情報を効率的に共有したり保管する際の手間がかかりにくくなったりします。ハンコも使わないか代わりに電子印を利用するなど対応すれば、業務の生産性が上がるでしょう。
ただし作業内容によってはアナログ作業の方が向いている場合もあります。たとえば工場で作業を行っており手が汚れた状態で、パソコンやタブレットを快適に操作するのは難しいでしょう。無理に電子化してしまうとすぐに機械が壊れたり、うまく利用できずに効率が悪くなったりと、かえってコストがかかってしまいます。
下図は厚生労働省が公開している資料を引用したものです。人手不足に関連した倒産は増加傾向にあり、特に2023年は「人件費高騰による倒産」が大幅増となりました。
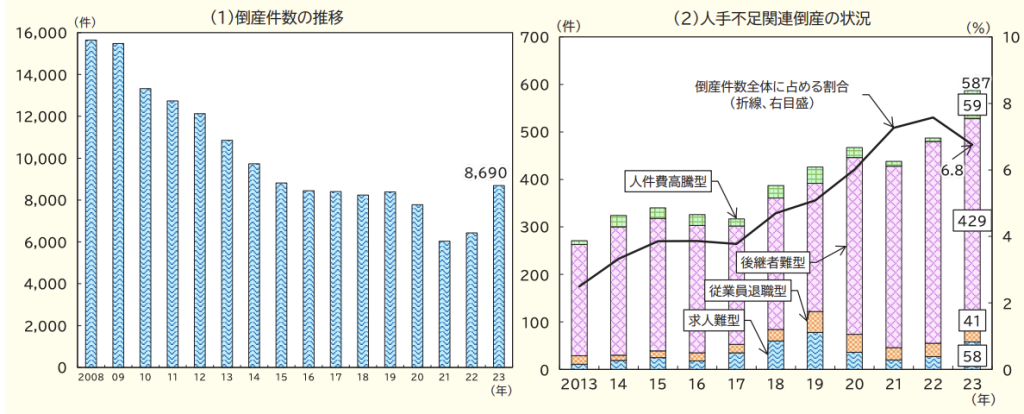
人には向き不向きがあります。たとえば現場で手を動かして働くのが好きな人もいれば、リーダーシップを発揮してチームを引っ張ったり仕組みを構築したりするのが好きな人もいるでしょう。
当たり前のことと思われるかもしれませんが、個人の適性を考慮した人材配置を実現できている企業は、多くはありません。なぜなら従業員の適性を一人ひとり見極めるのは手間と時間がかかるうえに、精度が良いのかどうか分かりにくいからです。
そこで人材アセスメントツール「ミイダス」では、適材適所の人材配置を実現するためのノウハウをまとめたお役立ち資料をご用意しました。下記から誰でも無料でダウンロードできるので、ぜひチェックしてください。
たとえば在庫を抱えすぎてしまうと保管するスペースを圧迫してしまい、作業場まで在庫が溢れてしまうおそれがあります。そうなると在庫が作業の邪魔になり、生産性が落ちてしまいかねません。
また仕入れが少なすぎると生産そのものを続行しにくくなり、こちらもボトルネックの発生につながります。ボトルネックを発生させないためにも適切な量の仕入れを行うことが大切です。
たとえば出荷する以上に製品を作りすぎてしまうと、在庫を保管するスペースを圧迫してしまいます。すると仕入れと同様、作業スペースが圧迫されてしまい生産性が低下するおそれがあります。需要を予測して適切な量の生産を行うことが重要です。
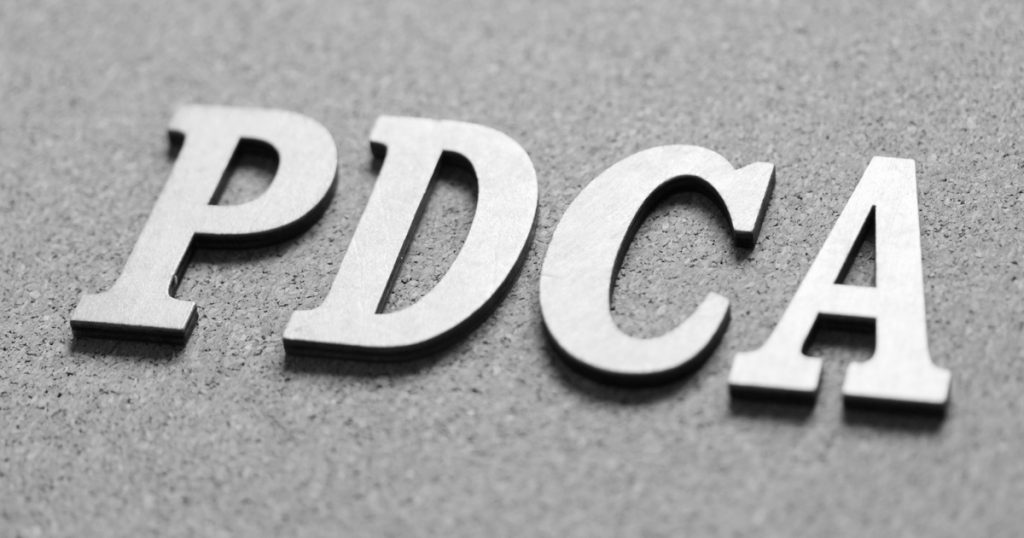
ボトルネック工程を発見する主な方法をご紹介します。
- 業務フローを可視化する
- データを分析して問題箇所を特定する
- 実際に現場を確認して問題箇所を特定する
それぞれ詳しく解説します。
業務フローを可視化する
業務の流れの可視化は下記のようなメリットがあり、ボトルネックを解消できる可能性があります。
- 工程ごとの関係性を可視化でき、無駄な工程を発見しやすい
- どの工程がどこに影響をするか視覚的に把握しやすくなり、工程の効率化を行いやすい
- 自分の担当工程がどのような影響を及ぼすのか把握しやすくなり、部署間の連携を強化しやすい
業務フローの可視化は、問題となっている工程の発見や効率化を行ううえで役立ちます。まずは作業の全体像を把握するためにも、業務フローを書き出してみましょう。紙やホワイトボードに書き出したり、タブレットのような手書き対応のデバイスにまとめたりするのがおすすめです。
データを分析して問題箇所を特定する
数字を根拠に問題箇所を発見するのも、ボトルネックを見つけるうえで役立ちます。
たとえば組立工程で、1時間当たり100個の製品ができると仮定しましょう。このとき製品の部品を製造する工程で、1時間あたり30個しか生産できていないとわかりました。すると、部品の製造工程がボトルネックになっていると特定できます。
たとえば組立工程で、1時間当たり100個の製品ができると仮定しましょう。このとき製品の部品を製造する工程で、1時間あたり30個しか生産できていないとわかりました。すると、部品の製造工程がボトルネックになっていると特定できます。
実際に現場を確認して問題箇所を特定する
現場に足を運んで問題はないか確認するのも、ボトルネックを特定するうえで有用です。
データ上は問題なくても、実際に製造現場を見てみると暇そうな従業員がいたり使われていない設備を発見できたりします。
データ上は問題なくても、実際に製造現場を見てみると暇そうな従業員がいたり使われていない設備を発見できたりします。
TOC理論を活用したボトルネック工程の改善方法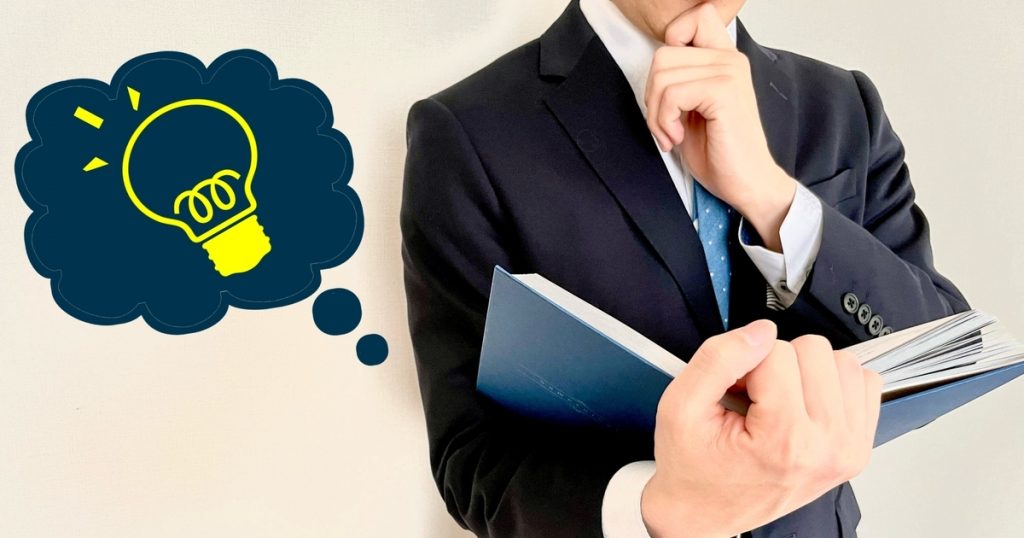
ボトルネックを改善する方法として有名なものに「TOC理論(制約理論)」というものがあります。TOC理論は「業務フローの制約条件(≒ボトルネック)を解消して全体最適化を実現できる」ことを示している考え方です。
TOC理論では下記の流れで改善を行うことで、ボトルネックを解消できると提唱しています。1. ボトルネックとなっている工程を特定する
2. ボトルネック工程のパフォーマンスを向上させる
3. 他工程をボトルネック工程に合わせる
4. ボトルネック工程をてこ入れする
5. 新たなボトルネック工程を発見・改善する具体的にどのようなことを行うのか解説します。ボトルネックとなっている工程を特定する
まずはボトルネックとなっている工程を特定します。
上述したようにデータを確認したり実際に現場を確認したりして、問題のある工程を発見しましょう。ボトルネック工程のパフォーマンスを向上させる
ボトルネック工程を発見したら、既存の設備・人員のままパフォーマンスを向上させるための方法を考えます。- 待ち時間が発生している人はいないか
- 動いていない設備、待ち時間が発生している設備はないか
- 無駄な作業が発生していないか
上記の観点から、既存の設備・人員のままボトルネックを解消できないか検討しましょう。データをもとに仮説を立てたり、実際に現場へ足を運んだりすることで、パフォーマンス向上のきっかけを掴める可能性があります。他工程をボトルネック工程に合わせる
ボトルネックを現状対応できる範囲で改善できたら、次は他の工程をボトルネック工程に合わせます。たとえば現状の生産量は下記のとおりだと仮定しましょう。- 部品生産:15個/時間
- 製品組立:30個/時間
- 検品:50個/時間
このとき、ボトルネックとなっている部品生産の「15個/時間」まで、部品組立と検品の生産性を合わせます。これによって生まれた余剰能力を、ボトルネック工程の解消に活用します。ボトルネック工程をてこ入れする
余った余剰能力を活用して、ボトルネック工程にテコ入れを行います。
具体的にはボトルネック工程の従業員を増員したり、古い設備やシステムを更新したりします。これによって生産性が向上し、ボトルネックの解消が期待できるでしょう。新たなボトルネック工程を発見・改善する
ボトルネック工程を解消できたら、次は新たなボトルネック工程を発見して改善できないか検討してみましょう。たとえば下記の場合は「部品組立」が新たなボトルネック工程といえます。- 部品生産:60個/時間
- 製品組立:30個/時間
- 検品:50個/時間
ボトルネック工程を発見したら再び「既存設備・人員のままパフォーマンスを向上させる」「他工程をボトルネック工程に合わせる」「てこ入れを行う」といった方法で改善を進めていきます。
これを繰り返すことで全体の生産能力が底上げされるはずです。ボトルネック工程をてこ入れ・改善する方法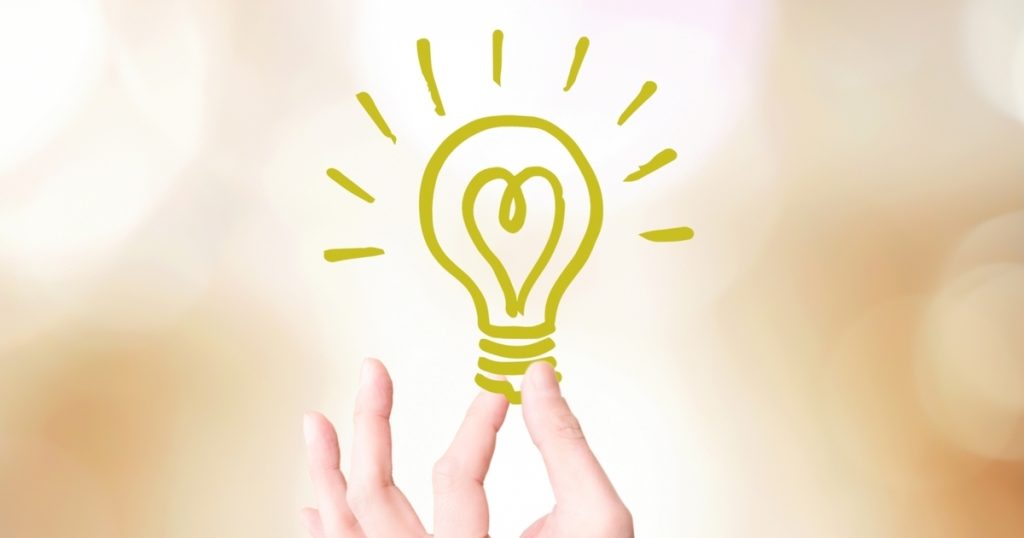
ここからはボトルネック工程をどのようにテコ入れして改善するのか、具体的な方法をご紹介します。- 適材適所の人材配置を行い一人ひとりのパフォーマンスを引き出す
- 新しい機械やシステムを導入して業務を効率化する
- より効率的な作業手順がないか検討して改善を試みる
- 人材を育成して一人あたりの生産性を高める
それぞれ詳しく解説します。適材適所の人材配置を行い一人ひとりのパフォーマンスを引き出す
ボトルネックを解消する方法の一つに、従業員のパフォーマンスを引き出すことが挙げられます。特に従業員一人ひとりの適性に合った人材配置を行っていれば、仕事へのモチベーションが向上したり成長速度が早まったりするはずです。
とはいえ一人ひとりの適性を見極めて人材配置を行うのは難しいかもしれません。担当した人事の能力によっても、成果が大きく左右されるでしょう。そこで人材アセスメントツール「ミイダス」では、適材適所の人材配置を実現するための具体的な方法についてまとめたお役立ち資料をご用意しております。
人事個人のスキルに依存しない、客観的に従業員の適性を見極める方法も紹介しています。適材適所の人材配置を実現するうえで役に立つ内容となっておりますので、ぜひチェックしてください。
【無料ダウンロード】適切な人事異動・配置をするための方法とは新しい機械やシステムを導入して業務を効率化する
新しいシステムや機械設備を導入するのも、ボトルネックを解消するうえで重要です。
何十年も使ってきた設備は、最新の設備と比較して生産性が低かったりトラブルが発生しやすかったりするものです。またパソコンをはじめとしたさまざまなデバイスのシステムを更新することでも、生産性の向上が期待できるでしょう。
工程を機械化すれば大量生産しやすくなるうえ、システム化・デジタル化を行えば情報共有の効率化や事務作業の生産性向上も期待できます。より効率的な作業手順がないか検討して改善を試みる
システム化や機械化に頼らず、より効率的な手順がないか検討してみることも大切です。
たとえば決裁フローが「部下→課長→部長」となっている場合、「部下→課長」または「部下→部長」に変更すれば、意思決定のスピードが向上するはずです。また「製造→検査→組立→検査→出荷」という作業フローの場合、「製造→組立→検査→出荷」という流れに変更するのも、効率化に役立ちます。
ただし必要な工程まで省略してしまうと、消費者からのクレームや商品の自主回収といったトラブルに発展してしまいかねません。省略できる工程かどうか見極めることも大切です。
無駄な作業を省いたり工夫次第ですぐに生産性が上がったりする方法がないか、検討してみましょう。人材を育成して一人あたりの生産性を高める
従業員を育成して生産性を向上させることも重要です。
たとえば工場作業の場合、OJTに加えて動画研修を実施したり、手順をマニュアル化して読ませたりする、といった方法で人材育成の質と量を向上できるでしょう。従業員が担当している仕事について理解を深めれば、生産性も向上するはずです。
従業員の教育をより効率的に・効果的に行う方法がないか検討してみましょう。ボトルネック工程を改善してビジネスを成長させよう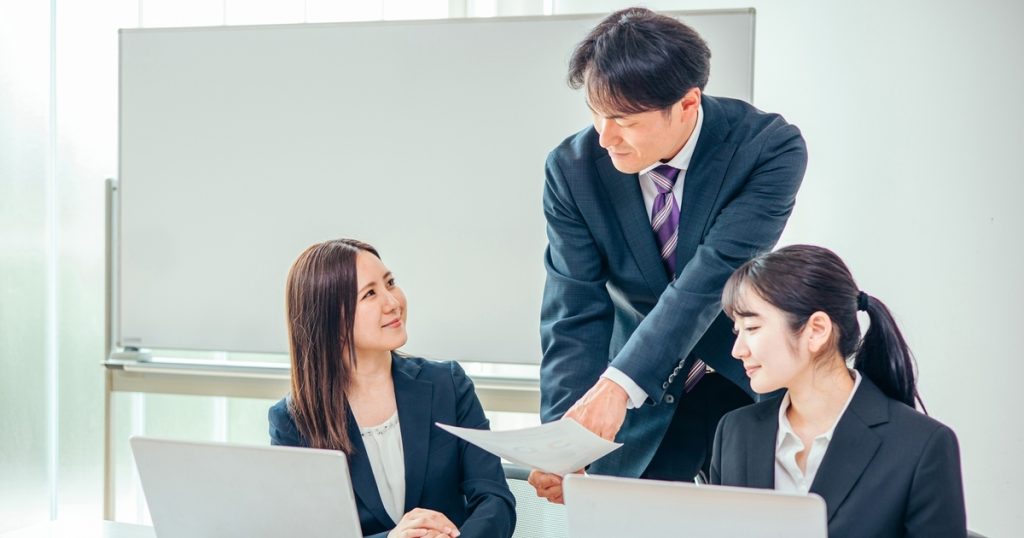
本記事ではビジネスにおけるボトルネックの意味や発生する原因、改善方法などをご紹介しました。
ボトルネックを解消できないと生産性が向上しにくく、企業の成長が鈍化してしまいかねません。ビジネスチャンスを逃さないためにも、ボトルネックの発見〜改善活動は継続的に行いましょう。
ボトルネックを解消するにはさまざまな方法がありますが、特に「適材適所の人材配置を実現する」ことをおすすめします。ボトルネックとなっている工程に適性のある人材を配置することで、作業効率が上がりボトルネックが解消する可能性があるためです。
とはいえ従業員の適性を一人ひとり見極めるのは手間がかかりますし、何より具体的にどうすれば良いのかお悩みかもしれません。そこでミイダスでは、適材適所の人材配置を実現するためのノウハウをまとめたお役立ち資料をご用意しました。下記からどなたでも無料でダウンロードできますので、ぜひチェックしてください。
【無料ダウンロード】適切な人事異動・配置をするための方法とは
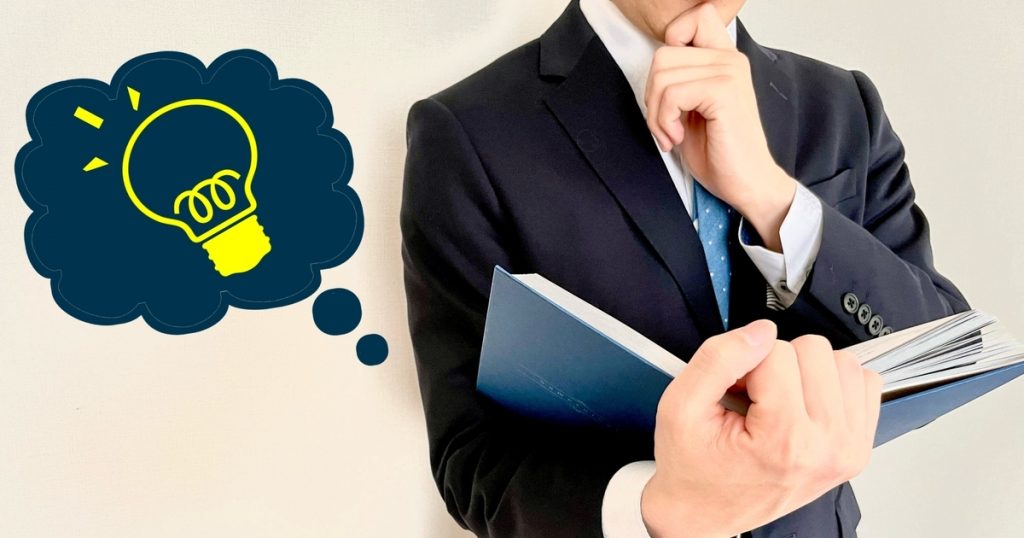
TOC理論では下記の流れで改善を行うことで、ボトルネックを解消できると提唱しています。
2. ボトルネック工程のパフォーマンスを向上させる
3. 他工程をボトルネック工程に合わせる
4. ボトルネック工程をてこ入れする
5. 新たなボトルネック工程を発見・改善する
上述したようにデータを確認したり実際に現場を確認したりして、問題のある工程を発見しましょう。
具体的にはボトルネック工程の従業員を増員したり、古い設備やシステムを更新したりします。これによって生産性が向上し、ボトルネックの解消が期待できるでしょう。
これを繰り返すことで全体の生産能力が底上げされるはずです。
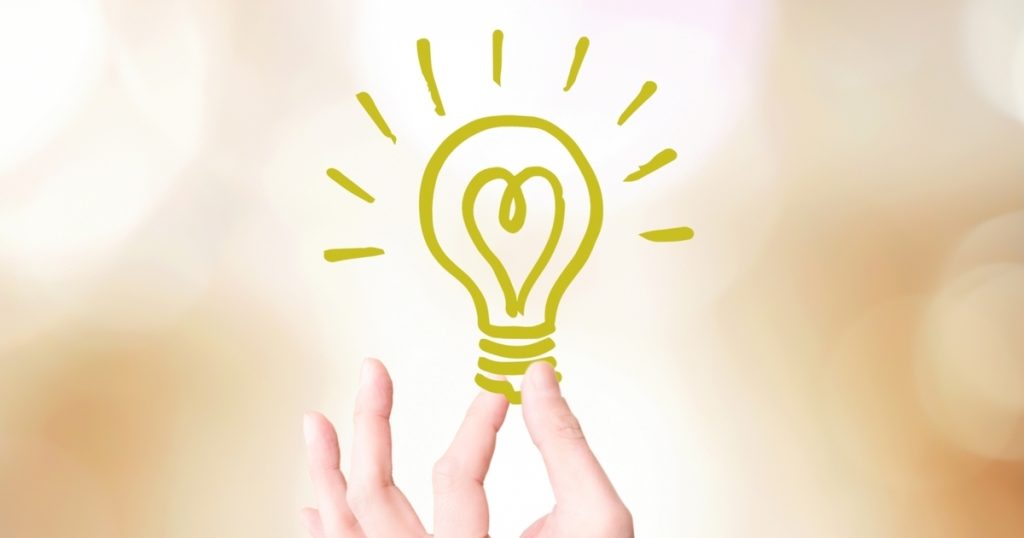
ここからはボトルネック工程をどのようにテコ入れして改善するのか、具体的な方法をご紹介します。
- 適材適所の人材配置を行い一人ひとりのパフォーマンスを引き出す
- 新しい機械やシステムを導入して業務を効率化する
- より効率的な作業手順がないか検討して改善を試みる
- 人材を育成して一人あたりの生産性を高める
それぞれ詳しく解説します。
適材適所の人材配置を行い一人ひとりのパフォーマンスを引き出す
ボトルネックを解消する方法の一つに、従業員のパフォーマンスを引き出すことが挙げられます。特に従業員一人ひとりの適性に合った人材配置を行っていれば、仕事へのモチベーションが向上したり成長速度が早まったりするはずです。
とはいえ一人ひとりの適性を見極めて人材配置を行うのは難しいかもしれません。担当した人事の能力によっても、成果が大きく左右されるでしょう。そこで人材アセスメントツール「ミイダス」では、適材適所の人材配置を実現するための具体的な方法についてまとめたお役立ち資料をご用意しております。
人事個人のスキルに依存しない、客観的に従業員の適性を見極める方法も紹介しています。適材適所の人材配置を実現するうえで役に立つ内容となっておりますので、ぜひチェックしてください。
とはいえ一人ひとりの適性を見極めて人材配置を行うのは難しいかもしれません。担当した人事の能力によっても、成果が大きく左右されるでしょう。そこで人材アセスメントツール「ミイダス」では、適材適所の人材配置を実現するための具体的な方法についてまとめたお役立ち資料をご用意しております。
人事個人のスキルに依存しない、客観的に従業員の適性を見極める方法も紹介しています。適材適所の人材配置を実現するうえで役に立つ内容となっておりますので、ぜひチェックしてください。
新しい機械やシステムを導入して業務を効率化する
新しいシステムや機械設備を導入するのも、ボトルネックを解消するうえで重要です。
何十年も使ってきた設備は、最新の設備と比較して生産性が低かったりトラブルが発生しやすかったりするものです。またパソコンをはじめとしたさまざまなデバイスのシステムを更新することでも、生産性の向上が期待できるでしょう。
工程を機械化すれば大量生産しやすくなるうえ、システム化・デジタル化を行えば情報共有の効率化や事務作業の生産性向上も期待できます。
何十年も使ってきた設備は、最新の設備と比較して生産性が低かったりトラブルが発生しやすかったりするものです。またパソコンをはじめとしたさまざまなデバイスのシステムを更新することでも、生産性の向上が期待できるでしょう。
工程を機械化すれば大量生産しやすくなるうえ、システム化・デジタル化を行えば情報共有の効率化や事務作業の生産性向上も期待できます。
より効率的な作業手順がないか検討して改善を試みる
システム化や機械化に頼らず、より効率的な手順がないか検討してみることも大切です。
たとえば決裁フローが「部下→課長→部長」となっている場合、「部下→課長」または「部下→部長」に変更すれば、意思決定のスピードが向上するはずです。また「製造→検査→組立→検査→出荷」という作業フローの場合、「製造→組立→検査→出荷」という流れに変更するのも、効率化に役立ちます。
ただし必要な工程まで省略してしまうと、消費者からのクレームや商品の自主回収といったトラブルに発展してしまいかねません。省略できる工程かどうか見極めることも大切です。
無駄な作業を省いたり工夫次第ですぐに生産性が上がったりする方法がないか、検討してみましょう。
たとえば決裁フローが「部下→課長→部長」となっている場合、「部下→課長」または「部下→部長」に変更すれば、意思決定のスピードが向上するはずです。また「製造→検査→組立→検査→出荷」という作業フローの場合、「製造→組立→検査→出荷」という流れに変更するのも、効率化に役立ちます。
ただし必要な工程まで省略してしまうと、消費者からのクレームや商品の自主回収といったトラブルに発展してしまいかねません。省略できる工程かどうか見極めることも大切です。
無駄な作業を省いたり工夫次第ですぐに生産性が上がったりする方法がないか、検討してみましょう。
人材を育成して一人あたりの生産性を高める
従業員を育成して生産性を向上させることも重要です。
たとえば工場作業の場合、OJTに加えて動画研修を実施したり、手順をマニュアル化して読ませたりする、といった方法で人材育成の質と量を向上できるでしょう。従業員が担当している仕事について理解を深めれば、生産性も向上するはずです。
従業員の教育をより効率的に・効果的に行う方法がないか検討してみましょう。
たとえば工場作業の場合、OJTに加えて動画研修を実施したり、手順をマニュアル化して読ませたりする、といった方法で人材育成の質と量を向上できるでしょう。従業員が担当している仕事について理解を深めれば、生産性も向上するはずです。
従業員の教育をより効率的に・効果的に行う方法がないか検討してみましょう。
ボトルネック工程を改善してビジネスを成長させよう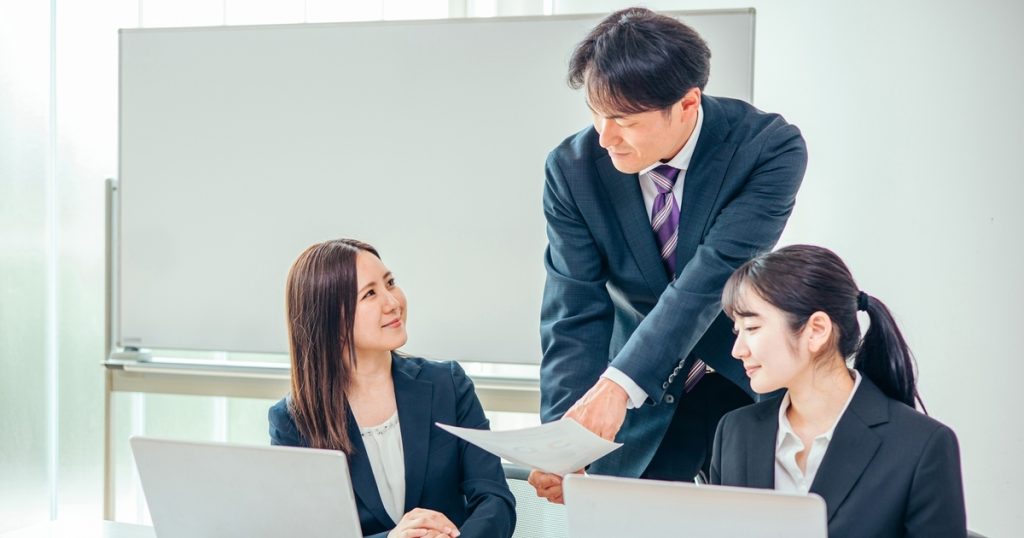
本記事ではビジネスにおけるボトルネックの意味や発生する原因、改善方法などをご紹介しました。
ボトルネックを解消できないと生産性が向上しにくく、企業の成長が鈍化してしまいかねません。ビジネスチャンスを逃さないためにも、ボトルネックの発見〜改善活動は継続的に行いましょう。
ボトルネックを解消するにはさまざまな方法がありますが、特に「適材適所の人材配置を実現する」ことをおすすめします。ボトルネックとなっている工程に適性のある人材を配置することで、作業効率が上がりボトルネックが解消する可能性があるためです。
とはいえ従業員の適性を一人ひとり見極めるのは手間がかかりますし、何より具体的にどうすれば良いのかお悩みかもしれません。そこでミイダスでは、適材適所の人材配置を実現するためのノウハウをまとめたお役立ち資料をご用意しました。下記からどなたでも無料でダウンロードできますので、ぜひチェックしてください。
【無料ダウンロード】適切な人事異動・配置をするための方法とは
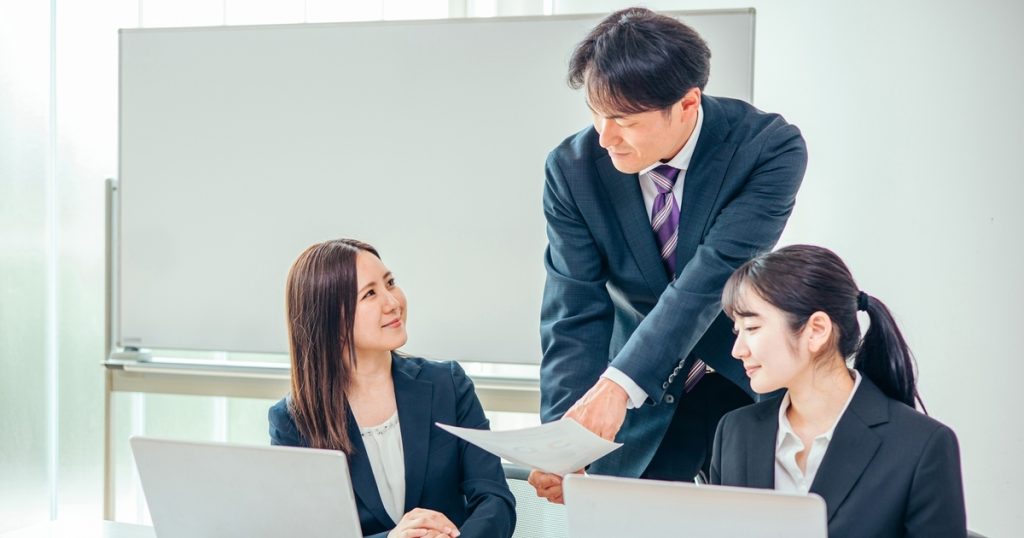
ボトルネックを解消できないと生産性が向上しにくく、企業の成長が鈍化してしまいかねません。ビジネスチャンスを逃さないためにも、ボトルネックの発見〜改善活動は継続的に行いましょう。
ボトルネックを解消するにはさまざまな方法がありますが、特に「適材適所の人材配置を実現する」ことをおすすめします。ボトルネックとなっている工程に適性のある人材を配置することで、作業効率が上がりボトルネックが解消する可能性があるためです。
とはいえ従業員の適性を一人ひとり見極めるのは手間がかかりますし、何より具体的にどうすれば良いのかお悩みかもしれません。そこでミイダスでは、適材適所の人材配置を実現するためのノウハウをまとめたお役立ち資料をご用意しました。下記からどなたでも無料でダウンロードできますので、ぜひチェックしてください。